Более чем 100-летний опыт технического прогресса позволил нам стать ведущим производителем в области частотных преобразователей, сервоприводов, систем управления и робототехники.
Highly flexible robot welding cell for maximum output
Robot duo masters 1,000 variants
Axles and frames for utility trailers, campers and mobile homes from AL-KO Vehicle Technology are among the best available on the market. Manufacturers all over the world place their trust in these components. Correspondingly high are the demands placed on welding technology, including first-class seam quality and highly flexible systems engineering with robots that operate with precision and process reliability.
The AL-KO Vehicle Technology Group is a global technology group. With high-quality body and chassis components for trailers, recreational and utility vehicles as well as construction and agricultural vehicles the group is a hallmark for best functionality, highest comfort and innovations for better handling safety. With a workforce of over 3,800 at 30 locations worldwide, the group reports an annual turnover close to a billion US dollars.
Despite the globalization and expansion of this successful company, the proven AL-KO trailer components – from overrun devices to the complete axle – are traditionally manufactured at its head office in the Swabian town of Kötz.
In particular the welds in frame manufacturing are subjected to high dynamic loads, and connecting these components is among the most demanding tasks in joining technology. A reliable welding process and state-of-the-art systems engineering are indispensable here, in order to guarantee maximum component quality while maintaining unrestricted flexibility.
For the manufacture of cross members for utility trailers with an overall weight of up to 3.5 tonnes AL-KO uses a new, pioneering welding cell in which two Motoman robots are engaged in parallel welding. The overall development of the welding cell is a joint project of AL-KO and Yaskawa. The starting point was a standardised specification by the Swabian manufacturer which predefined the key parameters, including energy efficiency, safety technology, process times and quality standards.
Maximum flexibility with minimum space requirements
Planning the installation became a real challenge due to two restrictions, as Steffen Schumacher, production and investment planner at AL-KO, reflects: “Firstly, very limited space was available for the complete installation, so that we had to be extremely inventive in order to realize the project at all. Secondly, the systems engineering had to guarantee a maximum of flexibility, as about 1,000 variants were to be welded by robot.”
Because only cross members for the aforementioned utility trailers were to be manufactured on the system, the extremely high number of variants may at first sound almost unbelievable. But if we consider that AL-KO serves over 50 small and large customers, this size is somewhat relativized. The spectrum is only limited by sheet metal thicknesses, which are between two and three millimetres.
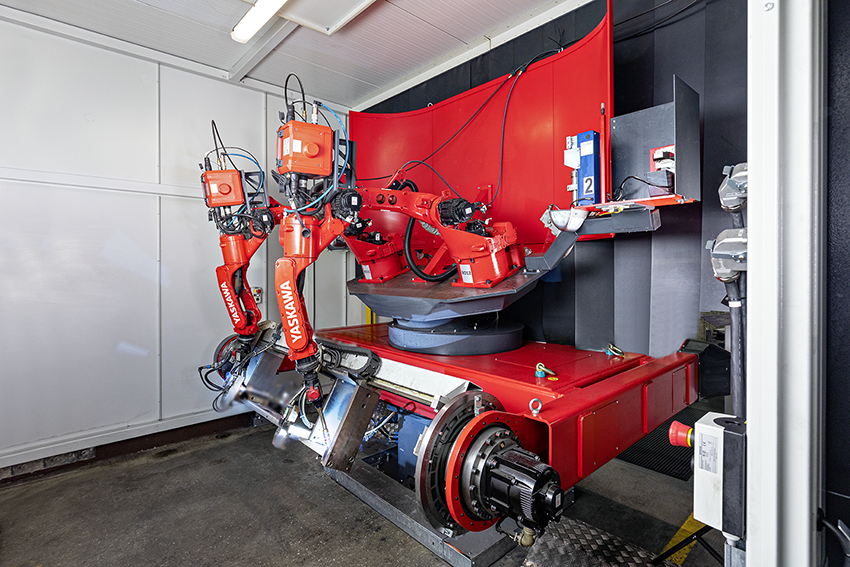
The concept of ultra-short delivery times
The company's claim to being able to deliver to customers within five days of placing their order calls not only for unbelievable flexibility, but also for the provision of corresponding manufacturing capacities together with extensive and expensive warehousing. Schumacher comments: “This customer service of short delivery times is, of course, a real challenge. However, customer orientation is also a unique selling point, appreciated by trailer manufacturers all over the world. Our task is to create structures with innovative production and intralogistics concepts that make this strategy of short delivery times possible.”
With the new welding unit, in which two slim Motoman Type MA1440 six-axis robots are in operation, AL-KO has shown how such solutions look in practice. Each robot has its own burner cleaner and wire cutter. The robot controller is a Yaskawa DX200. A three-axis H-table from Yaskawa’s standard programme serves as a positioner. The control of the complete installation is assumed by a user-friendly Siemens SPS S7, on which many welding programmes for the variants are now stored. The user only has to select a suitable programme and start the process.
The planners proposed an unusual solution to effectively compensate for the limited space. Yaskawa Sales Manager Roland Hermann remembers: “When we realised the extent of the spatial restrictions, it was clear in these circumstances that all registers would have to be pulled in order to find an easily accessible solution. Finally, the idea of mounting the two robots on the H-table led to success. The elevated working position of the robots also ensures perfect access to the welded assemblies. The complete cell is just 4.2 metres wide and 4.7 metres long.”
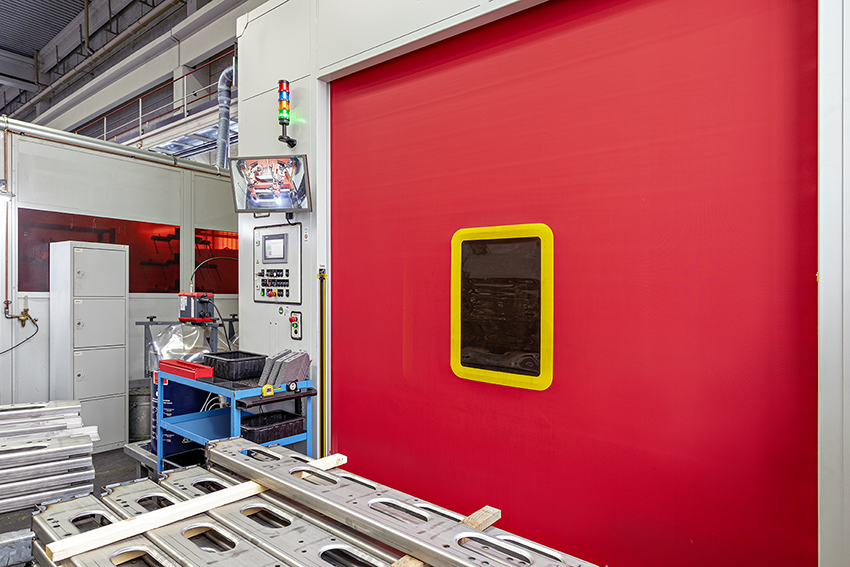
Top quality welding seams
Because AL-KO places a strong emphasis on weld seam quality, requiring that the welds meet the highest technical and visual standards, only premium welding technology was acceptable. “Specifically, we weld the holding brackets on the traverses, through which these cross-members are bolted to the longitudinal members of the trailer. This connection is safety-relevant, which is why a process-reliable, first-class welding result is vital here,” says Schumacher.
Not least because of this, the decision was made in favour of renowned manufacturer Fronius, which contributed both the welding power source TPS 500i and the water-cooled robot burner. The CMT technology employed here guarantees a largely spatter-free welding process with low component distortion.
Furthermore, the use of two robots radically reduces component distortion, although this solution was realised mainly due to the substantially shorter welding times.
Simple operation of the unit
There are no big surprises concerning operation of the unit: While the robots are welding on one side of the unit, an employee is busy with the removal of the finished parts and insertion of new components on the other side of the H-table. Cycle times vary considerably depending on the variant, but the removal and insertion work is always guaranteed to take less time than for the welding process itself. The Motoman welding robots can demonstrate their impressive dynamism to the full without waiting times. Downtimes are determined only by the rotation of the H-table.
As far as the batch sizes on the unit are concerned, the many variants are not exactly a positive factor. “Nevertheless, we managed to achieve an average batch size of 27. Roughly speaking, batch sizes lie between 10 and 100 components. Even smaller quantities are not really profitable to produce by automated means and, if unavoidable, these are manufactured by manual welding,” stresses Gökhan Kocak, AL-KO production manager in frame part manufacturing.
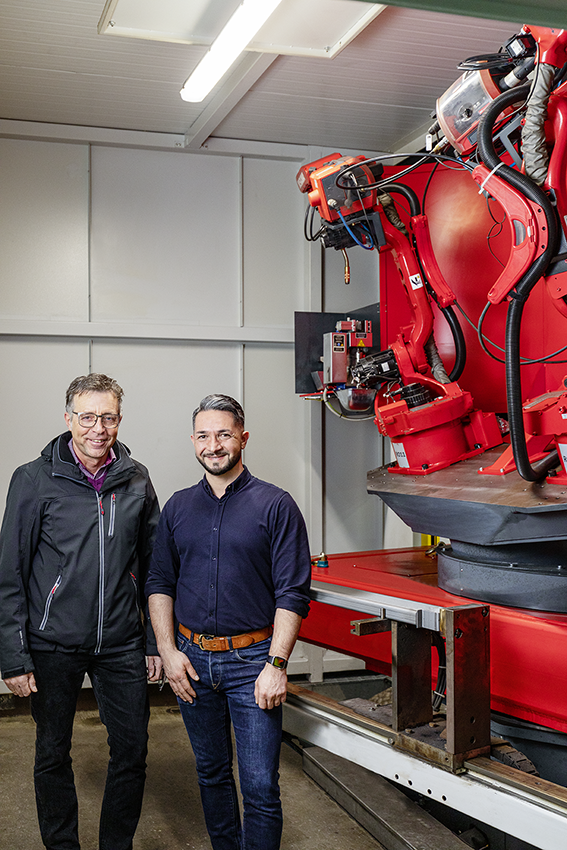
All targets met
The welding results reliably delivered by the unit do not fail to satisfy the high expectations. This is proven by first- and final part sampling, obligatory for every production order in frame part manufacturing. In addition, the system operator – responsible for manually loading and removal the parts – performs a visual inspection of each component.
Schumacher sums up: “As no other robot manufacturer, Yaskawa stands for welding quality and process reliability. The two welding robots demonstrate an impressively high level of dynamism and precision. Thanks to their slim design, they cope very well with the lack of space. All in all, with the jointly developed unit we were able to optimally meet our targets.”
Text: Ralf Högel
Contact readers’ enquiries
Tel. +49-8166-90-0
Fax +49-8166-90-103