Более чем 100-летний опыт технического прогресса позволил нам стать ведущим производителем в области частотных преобразователей, сервоприводов, систем управления и робототехники.
MQS develops robot-based component measurement with Motoman GP12
Production-oriented quality control in a matter of minutes
The precise measurement of larger components is so expensive that only random checks are usually possible. In the wake of constantly growing quality requirements, there is increasing pressure –particularly from the automotive industry – to significantly step up the measurement quota. An automatic measuring cell from Ingolstadt-based MQS AG now makes this possible. The new development is equipped with a high-performance Yaskawa Motoman GP robot.
Many industrial products must comply with particularly high standards, and call for precise and reproducible measurement in quality control. But while this can be accomplished with relative ease, e.g. for a safety-relevant screw, the measurement of larger components is much more complex. For example, a conventional coordinate measuring machine or strip light projection requires up to two hours to accurately measure a car door. Furthermore, the test piece must be removed for the production process, costing further valuable minutes.
Against this background, it quickly becomes clear that the measurement of such larger components in fast-cycled production processes cannot be accomplished by random inspection. However, this is in opposition to the urgent wish of many industries for increased inspection, ideally to 100%. The automotive industry strives for such continuous quality control. Due to the complexity of the task, suitable facilities for atline or inline measurement are largely lacking. The high precision expected from a coordinate measuring machine must be ensured in significantly shorter cycle times.
Industrial metrology systems and services specialist MQS AG in Ingolstadt has now risen to the challenge. The result of about 18 months of development work is a robot-based solution with the name MANTIS. A first demo cell has been in operation since November 2020, and the success is overwhelming. The system achieves in only a few minutes what used to take hours.
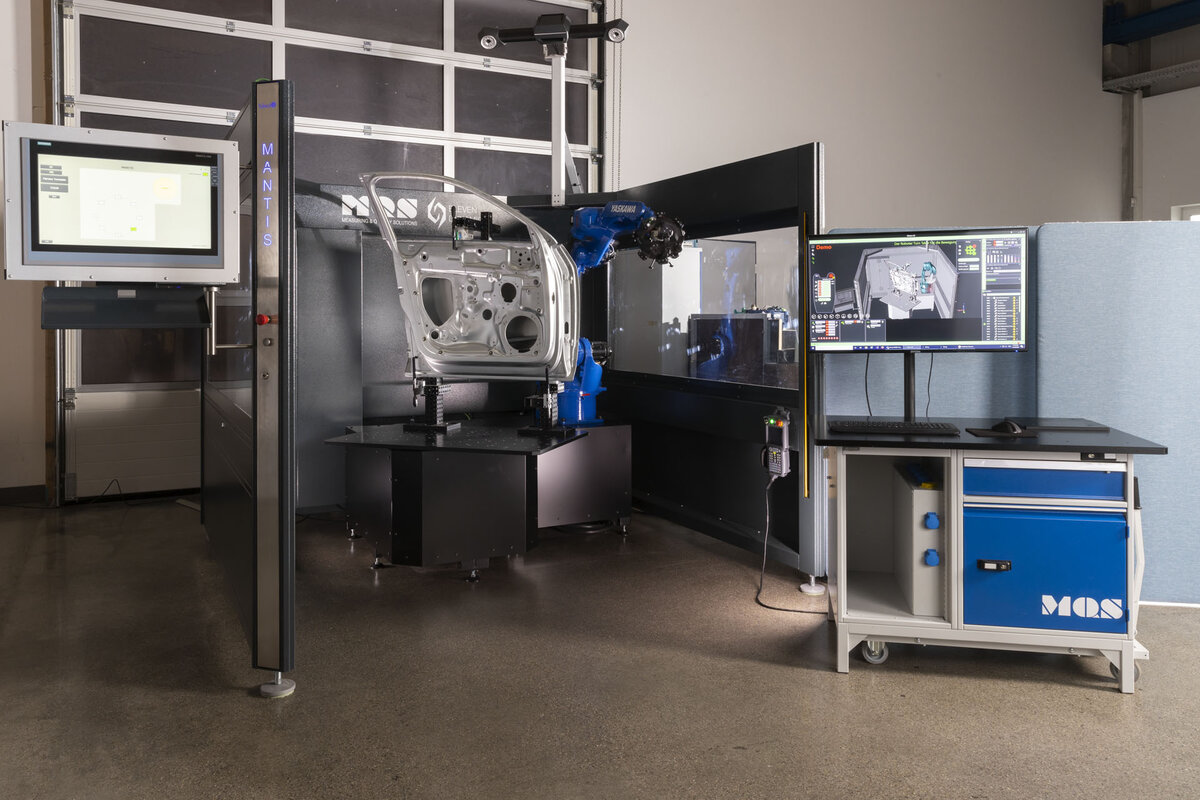
Fully integrable complete cell
The turn-key complete cell combines several elements: the measurement system itself, consisting of a measuring head (scanner) and a camera (tracker); a handling robot, on which the measuring head is mounted; and a rotary table for flexible positioning of the test piece. The camera positioned above the cell is reminiscent of a huge praying mantis – thus the name of the cell. “Mantis is the Latin term for the predator insect,” Andreas Zacherl, automation expert at MQS, explains the unusual name.
The measurement itself is performed by the measuring head, an upstream product of Scantech.Guided by the robot arm, it carefully scans the component being inspected. A total of three different lasers are in action. The camera permanently monitors the position of the measuring head. “The scanner thus always knows where it is currently located,” Zacherl describes the interplay of the two components. In addition, the scanner orientates itself at several marker points on the rotary table. This point cloud ensures that the measuring position remains precisely calculable after the test piece is rotated or moved. Currently, the system achieves a measurement accuracy down to three hundredths of a millimetre (1/100 mm). The measuring time for a car side door is about five minutes.
Besides the variously combinable hardware components, an application-specific, user-friendly software of development partner Eleven Dynamics constitutes the second pillar of the automated measuring concept. Automatic measurement takes place on the basis of stored CAD data or defined test points and measurement schedules. As an offline or online platform, MANTIS enables the integration of new technologies and scales the use of existing methods for future applications. The cell can thus be easily augmented by automatic loading or integrated into complete production lines.
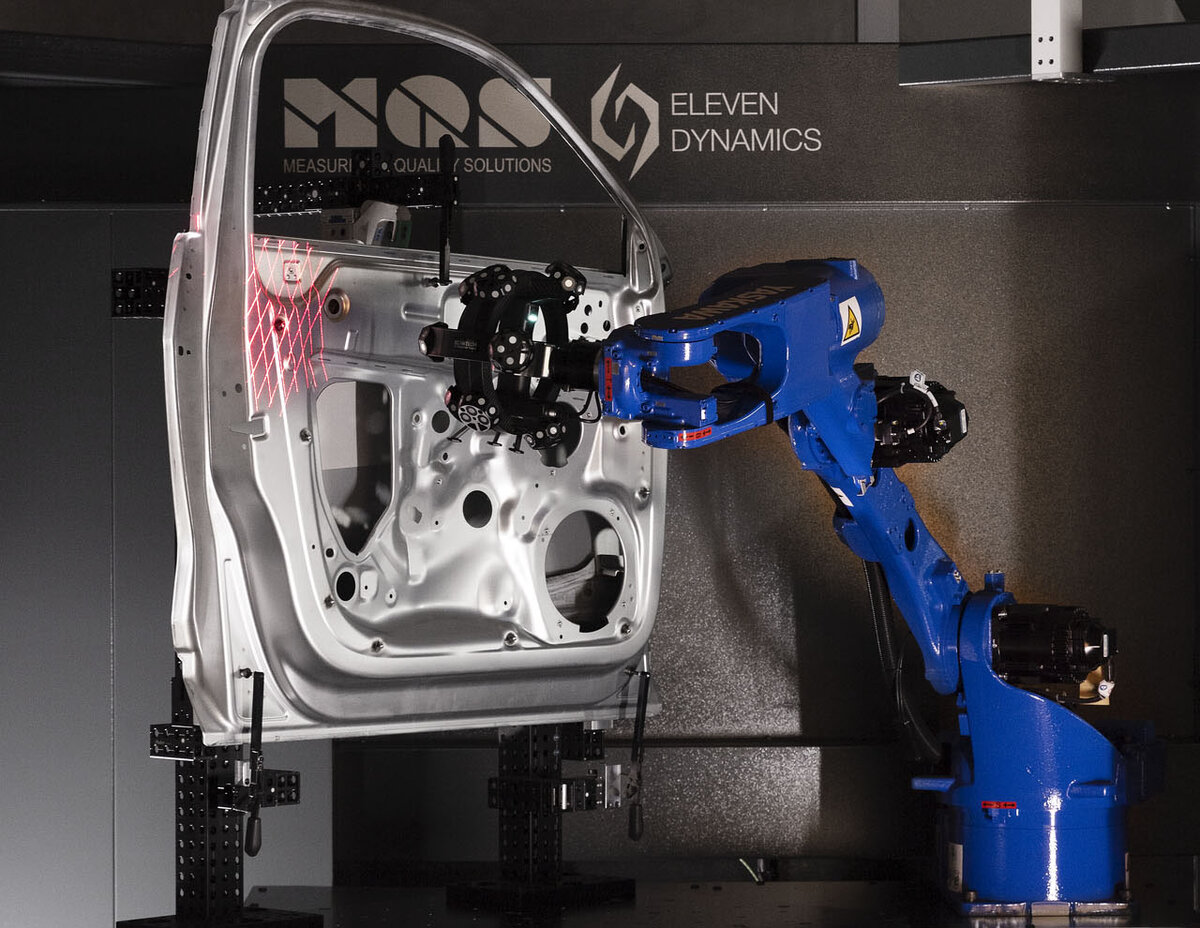
Motoman GP12 handling robot
The decision in favour of Yaskawa as a robot manufacturer was taken for a simple reason: “The proximity of the company provided the main impulse for initial contact. Allershausen is only half an hour by road from us,” Zacherl reflects. “In subsequent stages of the project we quickly learnt to appreciate the excellent cooperation.”
On Yaskawa’s advice, the choice fell on the Motoman GP series of handling robots. The principal deciding factor in this specific case was the high degree of manoeuvrability of the 6-axis robot: “The manipulator must be highly flexible,” Zacherl outlines the special requirements, “on the one hand in order to reach parts such as the underside of the object to be measured, and on the other hand to prevent the robot arm from blocking the measuring head or obstructing pick-up.”
The prerequisites for this are created by the slim arm design that minimises interference with the periphery. The hollow arm for internal wiring increases the stability of the media cables to the respective actuators, in this case to the measuring head. In all models of the GP series a single robot cable is required for the connection between manipulator and controller. The advantages of this solution lie in a less wear and easy maintenance. Furthermore, the start-up is fast and problem-free – particularly when integrated into a cable drag chain. High availability is guaranteed, even in harsh environments. The wrist axes of the robust robot in Protective Class IP67 and the main axes in Protective Class IP54 are standard features.
A Motoman GP12 was installed in the demo cell. The maximum payload of 12 kg was not a crucial factor here, as the measuring head is comparatively lightweight. Nor is the high positioning accuracy of the robot fully utilized due to the precise optical monitoring of the measuring head position. However, the Motoman GP12 offers a wide range of 1440 mm. For larger and smaller components, the Motoman GP series also includes further model versions with a range of 550 to 4004 mm.
The robots of the GP series are actuated by the new Motoman YRC1000 high-performance controller. Due to open interfaces, this generation of controllers is predestined for use in networked and industry 4.0 environments. The hand-held programmer of the YRC1000 controller – the lightest in its category at only 730 g – is ergonomically and clearly arranged. The touchscreen enables intuitive operation and thus simple movement and scrolling with the cursor. A 3D simulation of the robot movement prior to and during operation with the real robot arm can be followed on the display of the hand-held programmer. The extremely compact controller with a cabinet volume of only 125 litres permits optimum use of space.
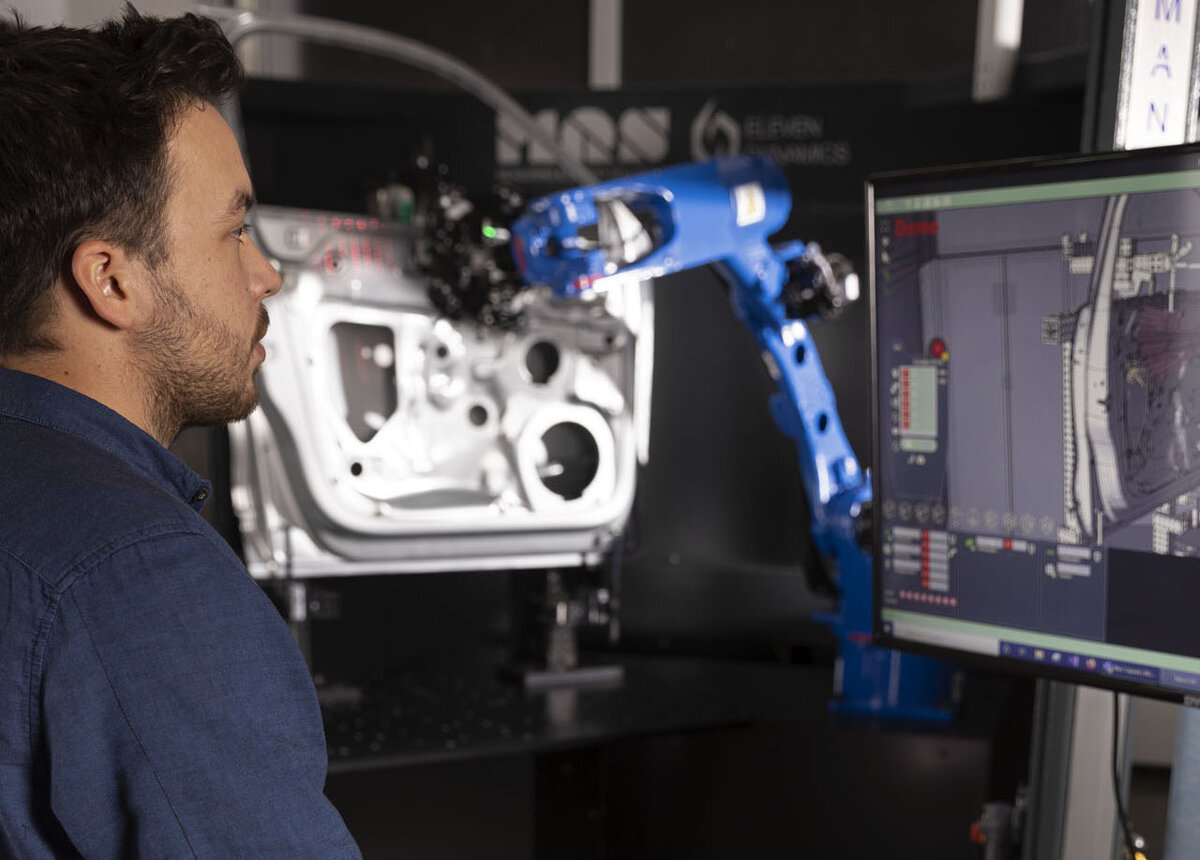
Summary
With the MANTIS the MQS AG of Ingolstadt has developed an automated and fully integrable turn-key solution for measurement technology – and a completely new concept for the smart factory of the future. The versatile robots of Yaskawa’s Motoman GP series are the ideal support for this concept due to their slim design, a wide range of models and open interfaces.
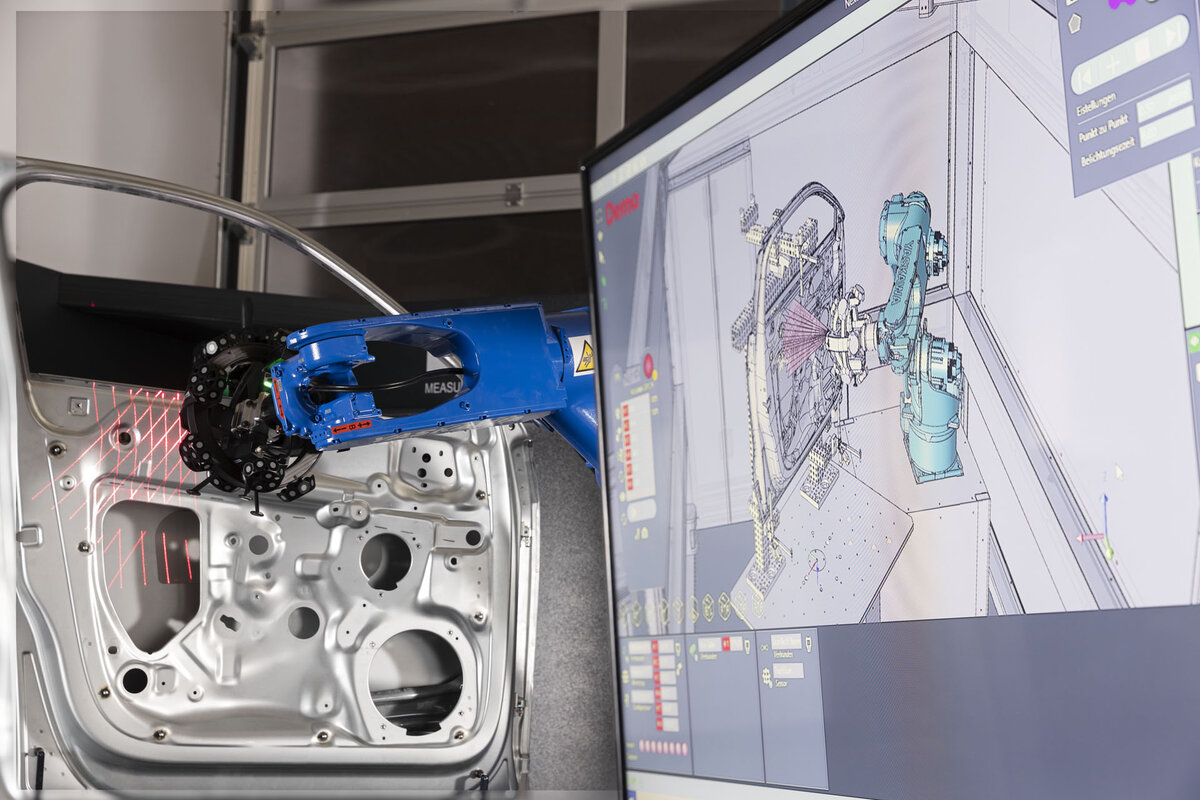
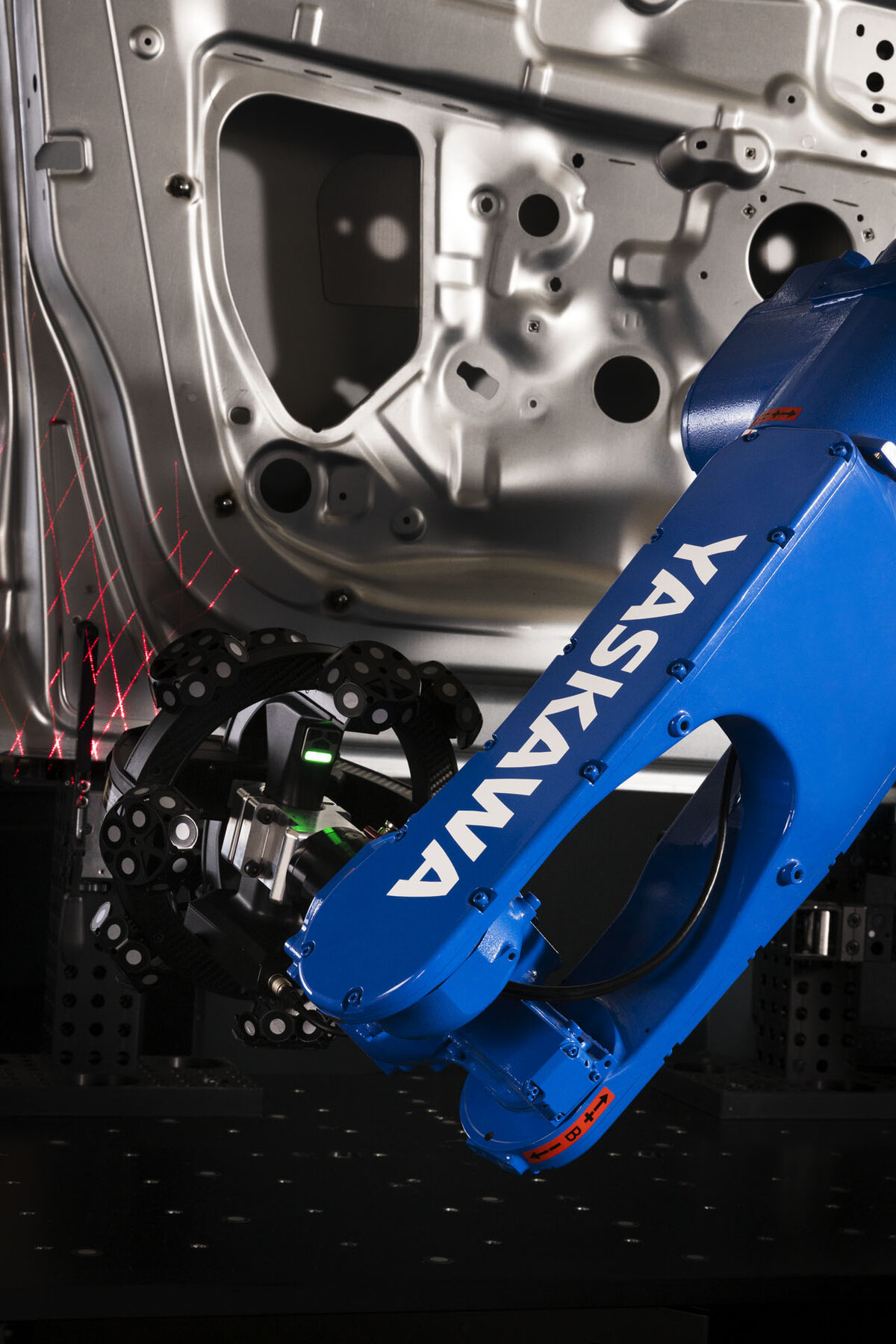