Более чем 100-летний опыт технического прогресса позволил нам стать ведущим производителем в области частотных преобразователей, сервоприводов, систем управления и робототехники.
Safe movement, even at great heights
Yaskawa inverters with dedicated functionality for driving large cranes
Very often, when we think of motion management and control applications, our mind immediately goes to systems on belts, rails or situations where the object to be transported is on a surface. However, when the load is suspended, a whole new set of variables comes into play. Dedicated drive functions can make a difference in ensuring clean and fast movements. Luigi Cattaneo SPA has chosen Yaskawa inverters for the motion control of its cranes, solving the pendulum problems that come with particularly long booms.
- Отрасли промышленности
- Construction
- Crane | Hoist
- Клиент
- Luigi Cattaneo SpA
A reference point in the world of cranes
Luigi Cattaneo SpA was founded in Magnago (Milan) in 1957 as a company specialising in the construction of tower cranes for the construction industry. Over the past 60 years, under the direction of the Cattaneo family, the company has become one of the most significant players in the field of tower crane manufacturers for the construction industry. For many years, Luigi Cattaneo has been a recognised point of reference for companies in their search for reliable, complete, modern and cutting-edge cranes. This is confirmed by the brand’s widespread distribution throughout the country and the constant growth of exports in Europe and the rest of the world.
The continual pursuit of advanced technological solutions plays a key role for the company, as does the expertise of its workers. One of the most recent technological optimisations has had a big impact on the control of crane movements in terms of boom rotation, trolley translation and load lifting.
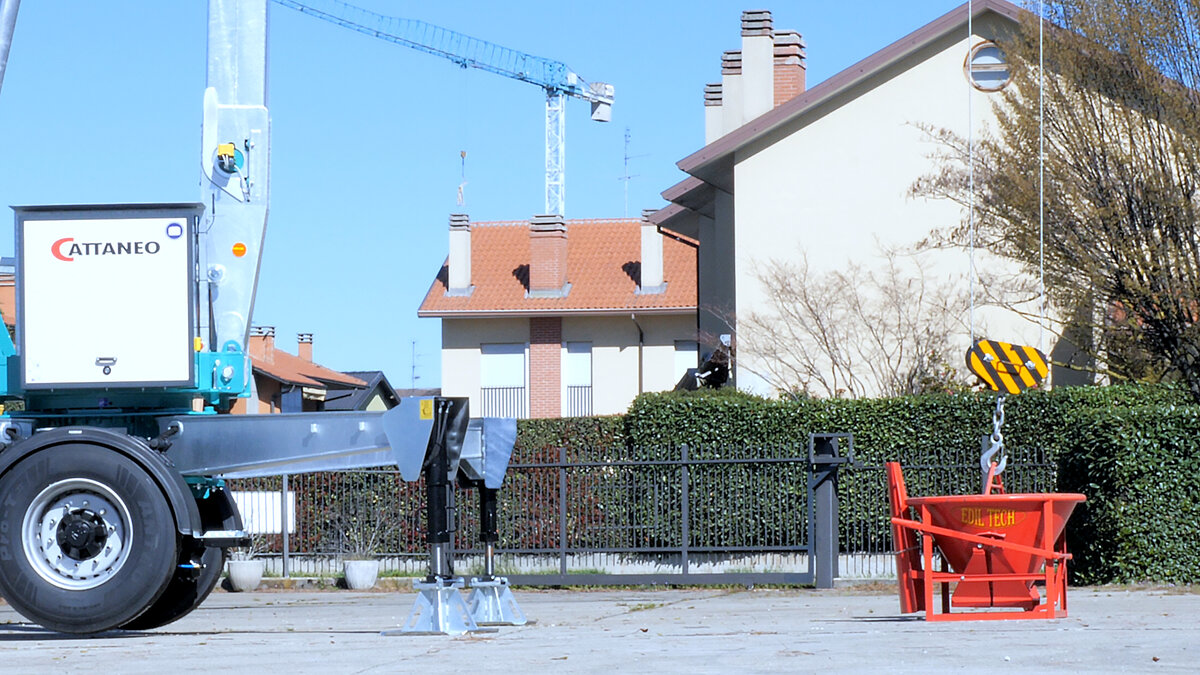
Demanding control for suspended loads
An intervention that is anything but minor, if we think of the importance of these movements: by lifting the hook, translating the trolley and rotating the arm, it is possible to pick up a load, move it both horizontally and vertically, and allow material to be unloaded from a transport vehicle or lifted and placed on a construction site.
The most delicate aspects of these functions come down to managing the start and end of the motion. Since the load hangs from a cable, incorrect management of the start and end of the movement could cause dangerous oscillations for the operators loading and unloading the materials. The oscillations are also damaging to the structure of the crane, both in terms of the fatigue strength of the steel and the stability of the crane itself.
Prior to this new and innovative intervention, this made it necessary to limit the movement speeds to avoid generating oscillations in both the load and the structure of the crane. Moreover, the positioning was always uncertain and imprecise, which meant that operators had to push the load sideways to position it correctly. There was therefore a clear need to make the movement faster and the load positioning more precise.
In order to solve these issues, Luigi Cattaneo carried out extensive research and opted for Yaskawa inverters for all three motion functions. The inverters have been customised with ‘anti-pendulum’ functions that prevent load sway, and offer various speed options, including very slow ones, to enable precise positioning.
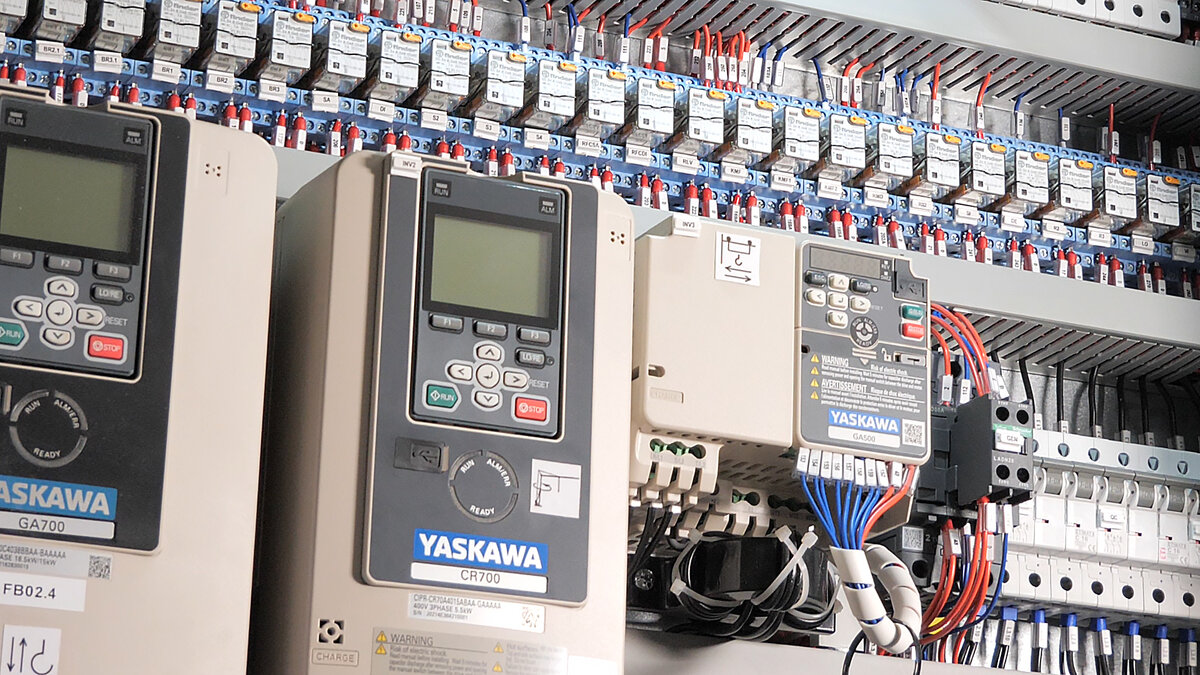
Linear movement control
The movement of the trolley is driven by a GA500, enhanced with a new overtravel management feature that uses a potentiometer located on the mechanism and managed by the inverter’s analogue input.
On the vertical axis, however, the application requirement for lower frequencies for power functions led to the initial A1000 device being replaced with a GA700, which has been enhanced with two dedicated functionalities. The Crane function – to manage the brake under certain speed and torque conditions by waiting for feedback from the brake contactor – and the UltraLift function – to maintain the desired power set point by reducing the reference speed, a highly important solution for single-phase machines, especially when the power supply is a 220-volt single-phase line.
Anti-sway specialist rotation function
The chosen solution for the boom rotation management system was twofold: for smaller cranes, a GA500 was selected complete with Brake Emergency frequency brake management, while for cranes with particularly long booms, a CR700 inverter with anti-sway function was chosen. This functionality ensures safe suppression of horizontal load sway without the need to add any external sensors or motor encoders. The result is reduced intervention times, maximum manoeuvring precision and increased crane efficiency.
The high-speed operability function also contributes to achieving these results by adjusting the operating speed based on the actual load. This can be done without the need for implementing load cells and sophisticated, expensive systems, simply by relying on the inverter’s internal software. Under light load, the drive increases the frequency reference and speed.
Particularly useful for handling certain rotations was the Advanced Open Loop Vector function, a new control patented by Yaskawa that has improved on the already high-performance classic vector control and allows for more effective control at low speeds to avoid load pendulum effects.
Customisation and optimisation
The versatility offered by the onboard PLC has made it possible to customise the software to best meet the application requirements. The task was handled quite smoothly: the customisation of the control software was carried out by Yaskawa personnel in close cooperation with Luigi Cattaneo’s technicians, while the ability to import function blocks between inverters without having to rewrite the entire project promised significant savings during commissioning.
The use of Yaskawa inverters also expands the possibilities of power supply: it can be provided by sources with very high voltages – even 480 volts continuous single-phase – or by generators without compromising the reliability of the product. It was precisely this feature that led the Cattaneo Gru engineers to develop an interesting energy-efficiency solution: the Eco Power function, which allows the power supply to be manually modified by lowering it from 21 to 16 kVA, for more environmentally-friendly use.
Finally, all Yaskawa inverters can handle 2 different motor curves, which means that the motor can also be used for assembly/disassembly with one of the 3 movements without having to insert a fourth inverter.